D. Nano-Electro-Mechanical Systems (NEMS)
Nanomechanics features three-dimensional nanostructuring, which allows full exploitation of the mechanical degree of freedom on the nanometre scale. An introduction to the underlying mechanics is given and finite element methods required for simulations are discussed. Further topics presented include measurement methods for probing the mechanical properties of free standing nanowires, sensor applications and nonlinear properties of nanomechanical resonators. Other applications such as parametric frequency tuning are demonstrated and the major sources of dissipation are discussed.
-
Nanomechanical Electron Transport
D. V. Scheible, A. Erbe, and R. H. Blick -
Mechanical gating of coupled nanoresonators
Laura Pescini, Bert Lorenz, Robert H. Blick -
Broadband acoustic tuning of nanomechanical resonators
Florian W. Beil, A. Wixforth and Robert H. Blick.
in cooperation with Max Bichler and Werner Wegscheider.
Nanomechanical Electron Transport
D. V. Scheible, A. Erbe, and R. H. Blick
The integration of nano-mechanical and nano-electronic systems promises very appealing applications in mesoscopic physics, ranging from current standard devices to detectors of ultra-weak forces. The concept of the quantum bell - a mechanically oscillating single electron island [1] - has been extended recently [2], including new driving methods and broader access to experimental parameters. Fig. 1 shows an excerpt of the device and the schematic testing setup, as well as the frequency-dependent current across the structure, being characteristic for resonant mechanical electron transporters. In addition to this, nano-mechanical electron shuttles also gain an increasing interest from the theoretical viewpoint [3].
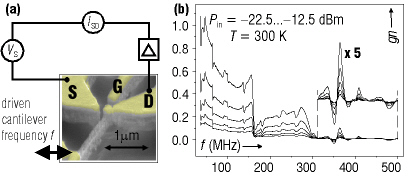
Figure 1.(a) An electron beam micrograph of the cantilever with a single electron island (Au) at its end. Driving this cantlever results in an oscillation of the island between source S and drain D contact. Maximum current transport occurs at frequencies f that match mechanical resonance (b). Shown is the average number of electrons gn shuttled each cycle.
- A Erbe, Ch Weiss, W Zwerger, and R H Blick, Phys. Rev. Lett. 87, 096106 (2001).
- D V Scheible, A Erbe, and R H Blick, New J. Phys. 4, 86.1 (2002).
- M Jonson and R Shekhter, Phys. World 16, 21 (2003).
Mechanical gating of coupled nanoresonators
Laura Pescini, Bert Lorenz, Robert H. Blick
We study the mechanical properties of suspended Au/Si nanostructures with focus on the interaction between mechanical nanoresonators operating in the rf regime. The actuation of the beams and their displacement detection is performed magnetomotively. The driving force is the Lorentz force which acts on the suspended device when an alternate current flows in the device and an orthogonal magnetic field is present. We find that the electromechanical coupling between two resonators allows to use one of them to effectively tune the frequency of the other. The deformation of the eigenmodes leads in fact to high frequency modulation of the capacitive coupling between the wires. This can be expressed by an additional term in the driving force, Fc(t)=C(t)V2(t)/d(t), where C(t), V(t) and d(t) are respectively the time dependent capacitance, potential difference and separation between the two wires [1].
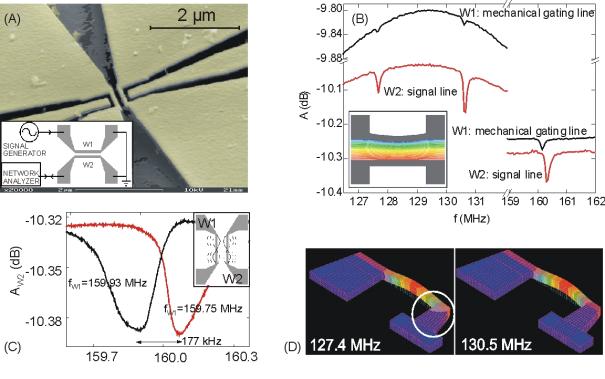
Figure 1. (A) Au/Si hybrid nanoelectromechanical system. The two nanoresonators are 80 nm wide, 920 nm long and their thickness is given by 100 nm Si + 40 nm Au. Inset: sketch of the measurement setup. While a network analyzer both drives and detects the displacement of resonator W2, a signal generator sends a signal of fixed frequency to W1. (B) The two resonators have very similar frequency spectra, i.e. they have almost identical eigenfrequencies. Inset: electrostatic field distribution between the two wires calculated with the computer program MAFIA. (C) Tuning of the signal line (W2) is achieved by applying a high frequency signal to the gating line (W1), as shown here for the two interacting modes at about 160 MHz, whose deformation is depicted in the inset. The two curves correspond to two different frequency values of the signal sent by the signal generator to W1. (D) Simulation of the deviceÓ³ eigenmodes performed with the program SOLVIA. The difference between the mechanical mode at 127 MHz and the mode at 130 MHz is that the former involves a portion of the support structure. This results in a higher effective length and consequently in a lower frequency.
- L. Pescini, H. Lorenz, and R.H. Blick, Appl. Phys. Lett. 82, 352 (2003).
Broadband acoustic tuning of nanomechanical resonators
Florian W. Beil, A. Wixforth and Robert H. Blick
in cooperation with Max Bichler and Werner Wegscheider.
For a variety of applications in integrated communication and sensor devices nano-electromechanical systems (NEMS) present a new generation of high frequency components. Up to now conventional excitation mechanisms for NEMS are based either on high magnetic (magnetomotive method) or electric (electromotive method) fields which limits the use of NEMS. We present experiments utilizing a surface acoustic wave (SAW) transducer on GaAs to excite nanomechanical resonators operating at frequencies up to 300 MHz. We show that via SAW full control over the fundamental properties of the resonator is achieved [1]. The quality factor of the mechanical resonance can be tuned over an order of magnitude, while by pulsed acoustic excitation an increased quality factor can be achieved. As acoustic tuning of internal damping mechanisms in the nano resonators is feasable, it is possible to determine the friction mechanisms [2] active on the nanometer scale.
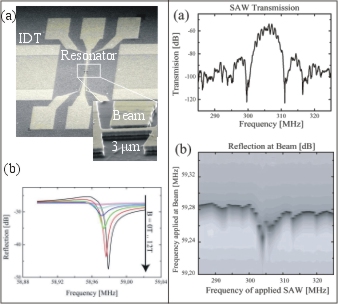
Figure 1. Left (a) Scanning electron micrograph of the freely
suspended beam placed in the line of fire of two interdigitated structures (IDT)
capable of producing a coherent acoustic beam at a definite frequency. (b) Magneto-impedance
spectroscopy of the beam resonator showing a resonance at 59 MHz. When decreasing the induced
Lorentzian forces by decreasing the magnetic field the resonance vanishes, proofing its mechanical
origin.
Right (a) Acoustic spectrum of the IDT delayline showing maximum acoustic
power generation at 305 MHz. (b) Interaction of the NEMS resonator operated at 59 MHz with the
surface acoustic wave at 305 MHz. When the additional acoustic field is applied to the beam the
resonance frequency an quality factor of the resonator are altered.
- F. W. Beil, A. Wixforth and R. H. Blick, IEEE Sensors (2002).
- F. W. Beil, A. Wixforth and R. H. Blick, to be published.